Cleveland Pump Repair offers pump repairs and servicing based on the following framework:
Repair Process
Cleveland Pump Repair follows a straightforward and efficient servicing procedure that optimizes your equipment in the shortest timeframe:
- Equipment is received and documented for file.
- The disassembly begins with visual inspection notes being documented.
- Now the components are thoroughly cleaned: various grit blast methods or liquid solvent cleaning.
- Formal inspection begins: Dimensional, NDE, Run-Outs.
- Inspection Report is developed and issued to customer – generally supported with pictures.
- A Recommended Repair Scope and Formal Quotation is developed for customer review, approval or modification
At this point, if desired, formal bid meetings may be required for competitive bidding of the repair. Or, on coordination with the customer, competitors can be received at our shop facility and provided the opportunity to review and inspect the equipment for the competitive bid process.
- Raw and Outsourced materials are ordered.
- Formal component repair routings are developed. These provide the specific instructions for the shop machinists and mechanics to insure the job is done correctly and in accordance with the committed repair scope.
- As repaired inspection data is collected: e.g. dimensional; NDE, as required; run-outs; balance; Hydro test, when required; special requirements; etc.
- Final assembly is completed.
- Paint and Preparation for shipment in accordance with customer requirements.
- Shipment is completed by commercial freight carriers or by CPR direct trucking.
- Repair invoice is prepared and sent.
- Repair records are filed for historical reference.
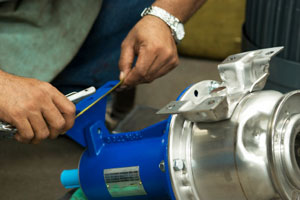
Contact a Cleveland Pump Repair Representative
Cleveland Pump Repair has built a comprehensive product lineup through partnerships with industry-leading manufacturers. Rely on us to provide the solutions you need to enhance your facility’s performance and efficiency.